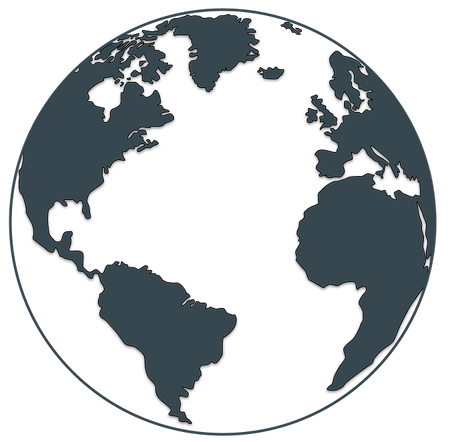
The planet is broken and we broke it.
We need to halve carbon emissions by 2030 and reach net-zero by 2050.
Let's not pretend anymore, business as usual isn’t going to get us there nor is changing light bulbs or any amount of sorting your recycling. We need significant, direct action.
I’m going to share a dirty secret with you…. The production of hydrogen today is made from fossil fuels and emits more CO2 into the atmosphere than the combined total emissions of Canada and Australia. That's the same as the global airline industry.
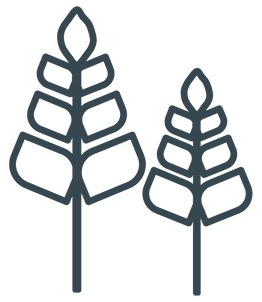
Companies with fossil fuels are planning to ‘just’ capture the emitted carbon but that's not working, live versions are still emitting more carbon than they are capturing (Blue Hydrogen).
So forget the flying hydrogen cars and the hydrogen coffee makers, just who is using all of that 90million tonnes of Hydrogen each year, worth £140billion? It’s the chemicals sector! With the biggest consumer being the ammonia process, which is mainly used for fertiliser and therefore the food on your table.
We don’t have to use non-renewable fossil hydrogen, there is a better way.
Electrolysers split water (H2O) into Oxygen (02) and Hydrogen (H2) using electricity.
All other electrolysers deliver gases at low pressure (20-40bar), requiring further compression to be useful, whether that’s to be stored, transported or used directly in a chemical plant like an ammonia production facility. The compression process adds more cost to the final delivered hydrogen. The reality of purchasing and operating compressors is conveniently ignored by most electrolyser companies today.
We saw the opportunity to create a step-change in real-world green hydrogen efficiency by building an electrolyser that outputs gas at a useful 200 bar pressure. i.e. the same pressure the biggest existing user of hydrogen requires.
You can’t just turn up the pressure dial on existing electrolysers, membranes would disintegrate and ceramic blocks would crack. We had to invent a new class of electrolyser, something completely new; something without a fragile membrane, which is the first point of failure on existing electrolysers. So that’s what we did!
Our unique technology can be used for the ultra-efficient production of high-pressure hydrogen. It also has other applications in waste processing, plastics recycling and even the production of carbon-neutral synthetic fuels. But our focus right now is the scaling of the technology with a demonstrator available in early 2023.
We are scaling our proprietary technology to serve the existing market of hydrogen. Today that is principally the chemicals sector. We can also transform medium to high heat industrial applications that are looking to switch from fossil fuels but cannot electrify feasibly or practically. Additionally, we can serve the heavy and long-haul transportation sector, where cargo weight and distances challenge battery solutions as alternatives to diesel. These markets combine to trillions in market cap and are responsible for 10 gigatonnes of CO2 each year; approximately one-fifth of the world's total greenhouse gas emissions.
Do YOU want to have a role that can have a direct impact on fixing the planet? Or are you content in a role doing nothing about it? We know we can’t do this on our own, we need talented and passionate people to join us.
If you would like to discuss how our technology can help you achieve your net-zero goals, get in contact, maybe you would like to be selected to be one of the first to pilot our technology in 2023.
Follow us on Linkedin and Subscribe to our newsletter.